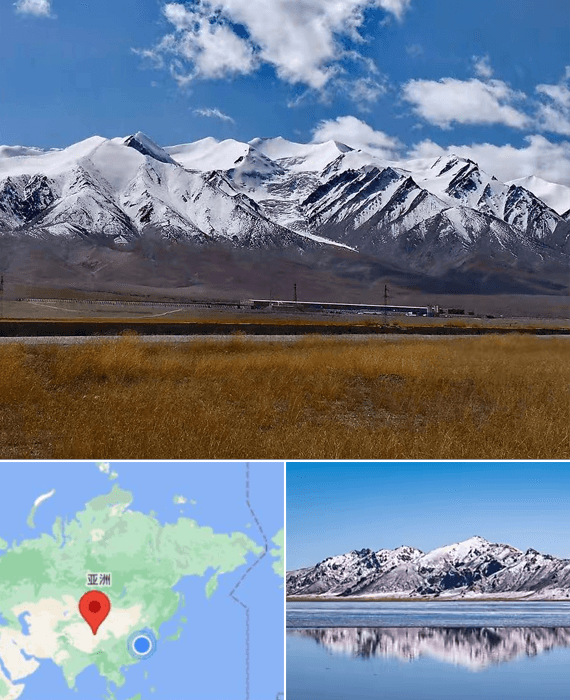
Where the red beet source material coms from ?
The red beet is planted in Qaidam Basin with average altitude around 3000m. It the important part of Qinghai-tibet Plateau,known as the roof of World. Qaidam basin is a plateau continental climate, known for its dry climate. The average annual relative humidity here is 30-40%, and the minimum relative humidity can be lower than 5%. Also,the temperature of this basin changes dramatically, with averange annual temperature is below 5℃.Unique geographical location creates unique quality.
Large difference in temperature between day and night is beneficial to plant accumulation of nutrients, improve the content of effective components,for example betalains and nitrates.
Ultraviolet intensity stimulates reduce disease caused by bacteria and insects.
Beets are nourished by the melting ice water of a thousand-year-old iceberg.
How it was grown?
-
Level soil
Before sowing, we need the land to be loosened and leveled. Under intense ultraviolet light, the bacteria inside are suddenly killed to improve the survival rate of the seeds.
-
Ridge planting
The typical ridge planting form of beet was ridging first and sowing later.Ridge cropping can make the soil voidness large, not easy to compact, conducive to crop root growth; The surface area of ridge cropping increases by 20%-30% compared with that of flat land, and the daytime soil temperature increases by 2~3°C compared with that of flat land, and the temperature difference between day and night is large, which is conducive to the accumulation of photosynthetic products.
-
Sow
We use the seed of Bejo company for seeding in compliance with None-GMO.
-
Fertilization
less fertilizer is used during planting. After harvest, the beet leaves can used as a natural fertilizer.
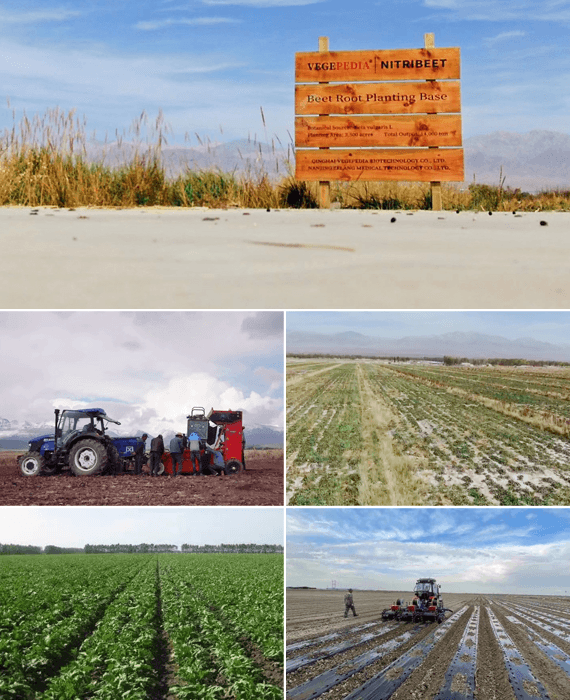
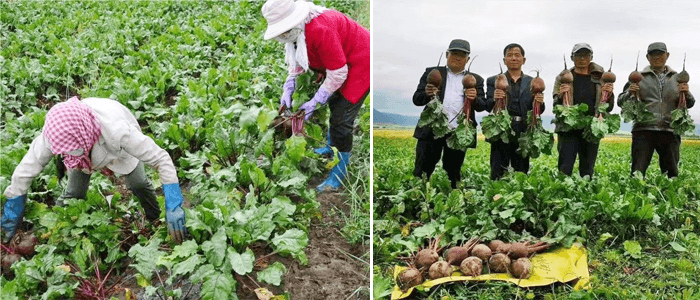
How it was harvest?
Harvest time: The best harvest time for red beet is from late September to early/middle October.
Manual harvesting: Machine harvesting is efficient, but it is easy to cause red beets to be mechanically injured. As a result, damaged beets can be contaminated with microorganisms. Manual harvesting is a gentle way of harvesting that prevents beets from being damaged before processing.
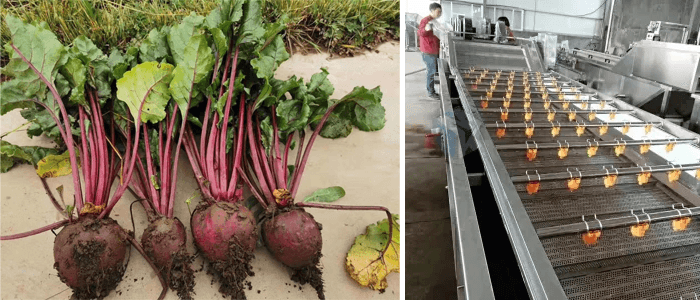
How it was selected?
Uniform size (2kg): Choose fresh beets of good quality and uniform size, weighing about 2kg as raw materials (beets of different sizes at different maturity stages have different active ingredients)
Seven steps for cleaning: Traditional cleaning is five steps; While,we adopt seven steps for cleaning.So the ash content and microorganismm can be effective controlled. All the beet will pass the metal & foreign materials detecting after cleaning to heavy metal, for example Pb.
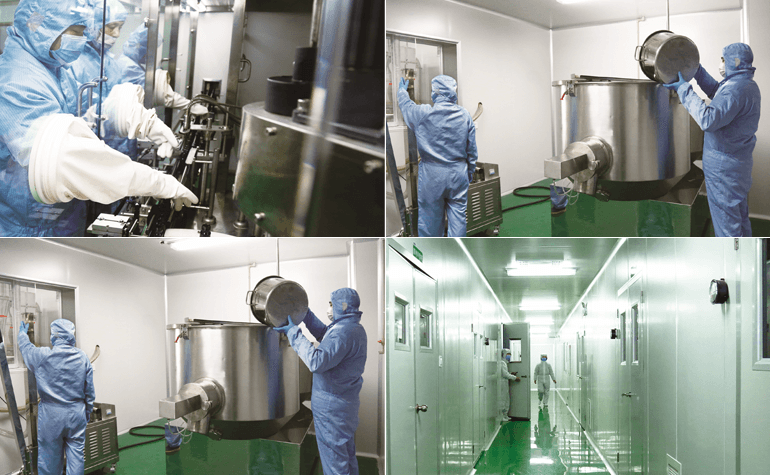
How it was processed?
Adopting size of 5*5*5mm: Cutting the cleaned fresh beet into 5*5*5mm size.Compared to the size of 10*10*10mm beet after cutting, the size of 5*5*5mm beet after cutting has a larger specific surface area. As a result the heating time is 2/3 of the 10*10*10mm. Effective in avoiding damage to the active ingredients of beets caused by prolonged drying.
Drying by Low temperature: The traditional drying temperature is 100℃-130℃, in order to protect the effective ingredients of beet; we take low temperature drying, about 85℃.
Grinding by Low temperature:The long crushing time will cause the temperature of the beet powder to rise, resulting in agglomeration Compared to10*10*10mm,5*5*5mm particles is featured bylow moisture, uniform size, which is easy to be crushed,with reducing the grinding time. Two-step crushing can also effectively reduce the crushing time. Water cooling and air cooling are designed in the production line to ensure that the beet material is below 50℃ during the whole grinding process.
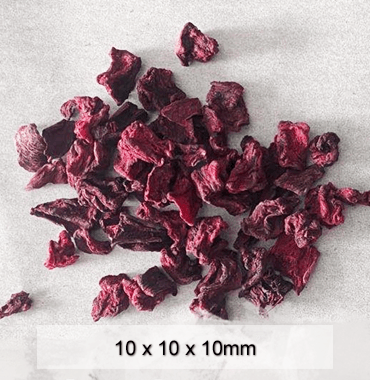
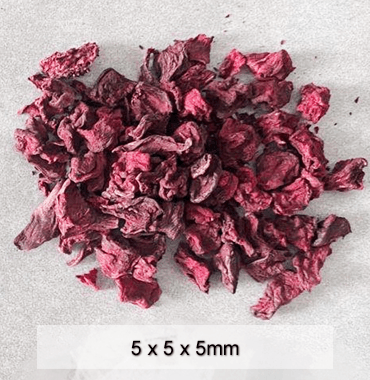
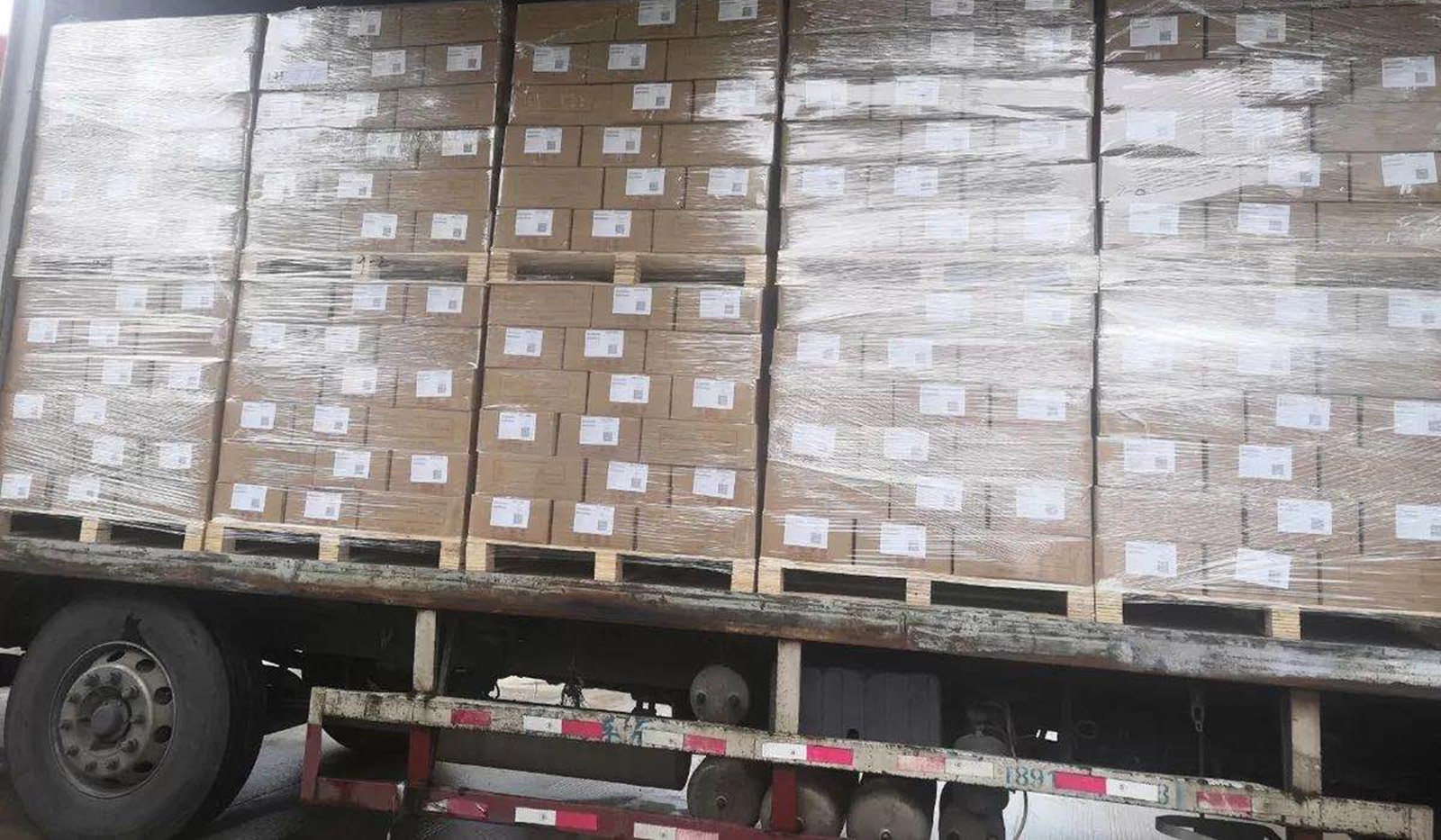
How it was packed?
The packaging of beet powder is carried out in the 100,000-grade purification workshop. The packaging material is recyclable aluminum foil bags and environmental cartons.
How it was shipped?
Packing well and short-distance: Packing and wrapping film before transportation, in order to avoid being damaged and polluted during transportation. We will transport the goods to Shanghai port by food truck. Our factory is 300KM away from Shanghai Port.
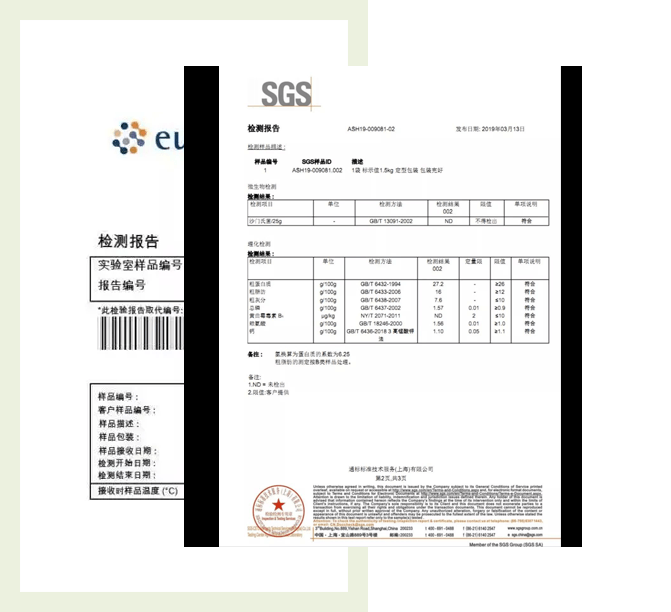
How it was tested and validated for potency?
Internal & extenal testing, Testing are done both during and after processing as per specification data sheet. At the same time, we also entrust third-party testing agencies, such as SGS, eurofins, to verify our test results.
List of Traceability documents
- Agricultural residues test report
- Heavy metal Detection Report
- Moisture test report
- Ash detection report
- Acid Insoluble Ash detection report
- Microbiological test report
- Nitrate report 20170301
- Nitrate report 20190702
- Nitrate report ZL20190709CR
- Nitrate report Zl20180409cr
- Nitrate report 20191220
- Nitrate report MZL20210707ZL
- Nitrate report 20210904
- Nitrate report 20210913
- Nitrate report ZL20210926D
- Factory procedure document
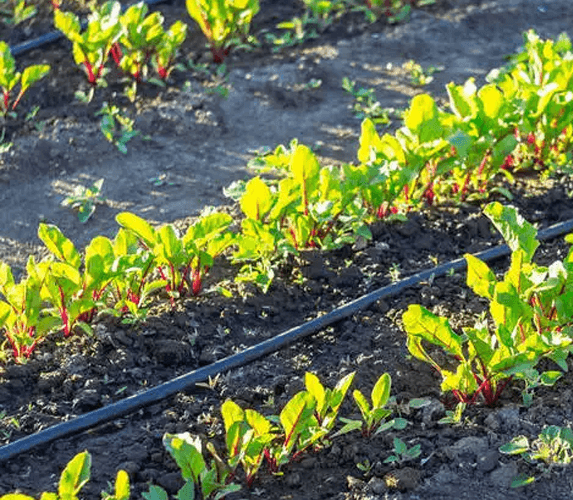
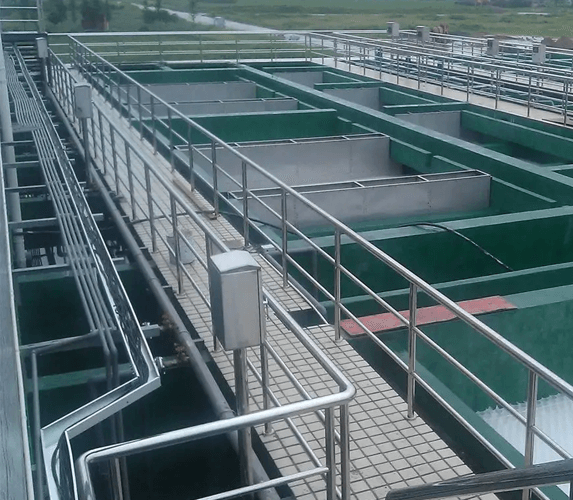
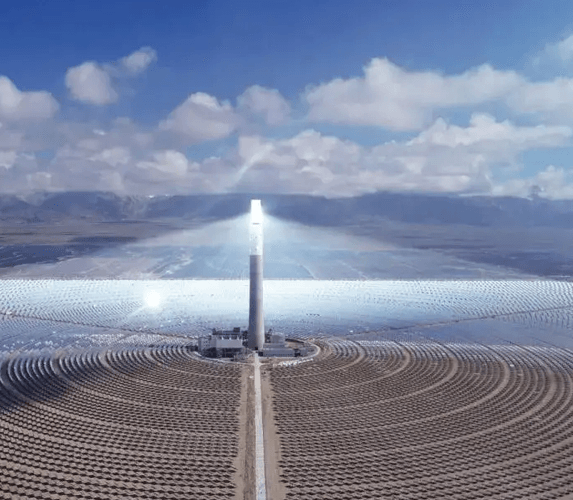
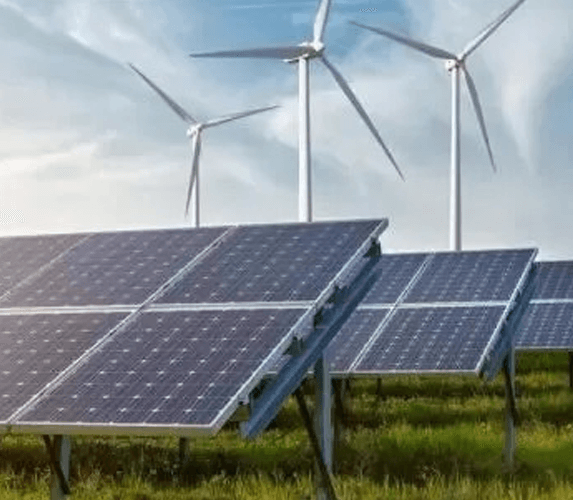
Carbon neutral and green initiative
List of Sustainability documents:
- Green environmental protection initiative
- 2021 Cleaner Production Audit and Acceptance List of Key Enterprises
Heating time
Reduce carbon emissions through process design. Cut into 5*5*5mm size of uniform shape particles (generally diced particles are 10*10*10mm, but 5*5*5 particles, the specific surface area is larger, heating time is 10*10*10mm particles 2/3, compared with the general enterprise carbon emissions reduced by 33%.
photovoltaic power
Use photovoltaic power generation instead of thermal power generation to achieve zero carbon emission.
Natural fertilizers
Chemical fertilizers are widely used in agriculture. In addition, the production of chemical fertilizers uses a lot of energy. We use natural fertilizers instead of chemical ones to reduce carbon emissions indirectly.